THE RECYCLING PROCESS OF PLASTIC
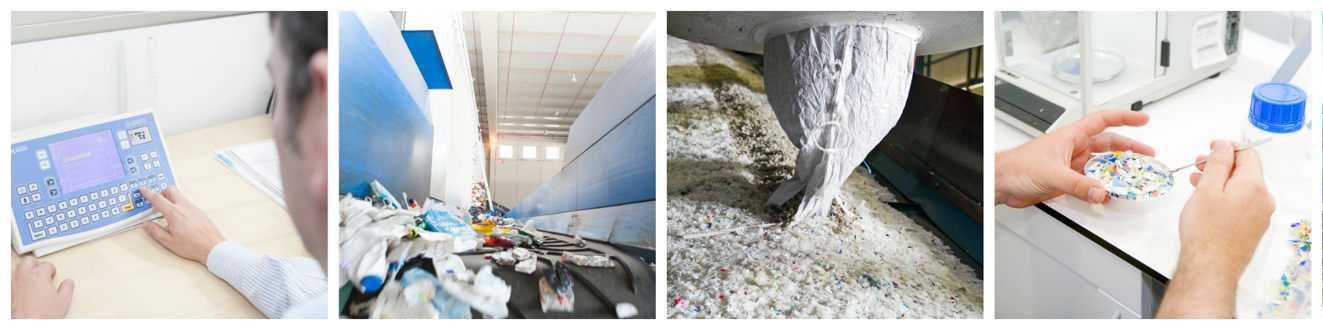
Our plastic recycling process can be divided into several phases:
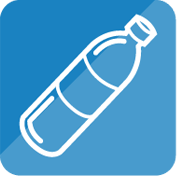
“Raw materials” means any plastic material that can be recycled (HDPE, LDPE, PP, PET, PS, ABS, etc.) in our facilities. The material must be presorted based on quality, and may come from industrial rejects or agriculture, or be post-consumer waste. These materials may come to us in boxes, sacks, big bags, shredded or in (bulk) containers or bales.
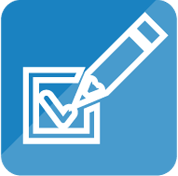
Once received, our raw material goes through a rigorous sorting process comprising the following phases:
Separation of unsuitable materials, based on type:
Any plastic materials different to those being processed at the time, in terms of quality, labels, iron-based materials, soil, etc., are separated out. This process helps us to ensure optimum quality while we increase production capacity and avoid inefficient production, and it serves as a way of monitoring the raw material provided by our supply sources.
Separation of plastic colours to be used:
This phase, allows us to use less dye, resulting in increased benefits both in economic and environmental terms. It also allows us to offer a wider variety of colour palettes in our finished products.
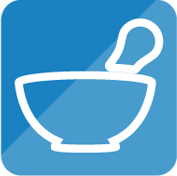
The pieces are broken down and shredded with high-production-capacity shredders using a set of rotary blades, and reduced to small pieces, depending on the diameter of the holes in the sifter. Shredding enables us to ensure that the particle size of the plastic is homogeneous, simplifying the subsequent transport, washing and drying work.
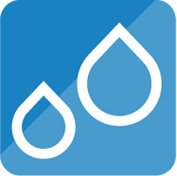
Once shredded, the plastic is loaded into industrial washers. There are blades that move the water so that the plastic is completely soaked; any impurities such as dirt, stone, metal, cardboard, PVC and any other material that is denser than water will fall to the bottom of the washers.
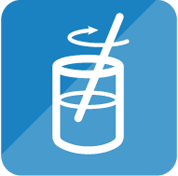
The material extracted from the washers then moves on to the spin dryers where – in addition to drying the plastic – any impurities that might have been missed during the washing phase are eliminated.
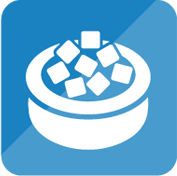
Once shredded, washed and dried, the plastic is stored in a large silo, where it will be mechanically mixed until it becomes homogeneous in colour, texture and behaviour, and is ready for extrusion
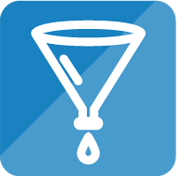
The central body of the extruder is made of a long barrel that, by means of the heat and friction of its interior shaft enables all the previously made particles to be plasticised, resulting in a uniform mass. This is how the polymers are melted by heat. It is in this stage that we add whatever colour is needed, based on the requirements of our clients in order to meet their needs.

With the required texture and fluidity, the plastic still undergoes a filtering process, a system of very fine meshes that will catch and hold any impurities that may have remained attached to the material during the earlier processes: cardboard debris, bits of wood, fabric or any other incompatible materials. When these meshes get dirty, they are automatically replaced by clean ones.
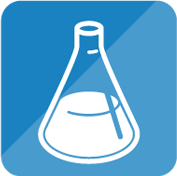
The plastic exits the extruder head as monofilaments or threads that, once in contact with the water in the water bath, cool. The strings pass through the noodle-type cutter, where they are sliced by a rotating knife. This process gives us the correct piece or regrind requested by our clients for their needs when buying regrinds.
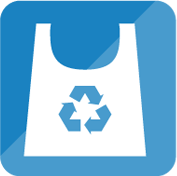
We divide the regrind production into batches. We then carry out laboratory analyses on samples from each batch on its characteristics in terms of smoothness, density, ash… thereby ensuring that our products are consistent in quality.
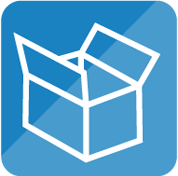
The regrinds are thrown from the extruder via a pneumatic system that uses an electric fan to a tank or silo where a cyclone will remove any remaining moisture. Later, based on the express needs of each client, the product is packed in 25-kg sacks or big bags.
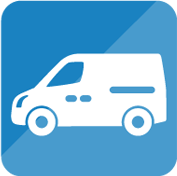
Storing the finished product properly is essential to avoid any potential damage: blows, severe weather conditions, deterioration, etc., and to attain the highest level of client acceptance.
Our capacity for storing finished products covers more than 10,000 m2 and enables us to provide suitable handling for the wide range of products manufactured in our plant facilities.
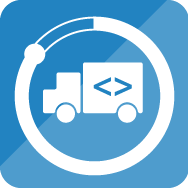
The material is ready either for pick-up by our client or for delivery to its destination, thanks to our nation-wide fleet of industrial vehicles.